6 Ways to Elevate Customer Satisfaction in Custom Equipment Design & Manufacturing
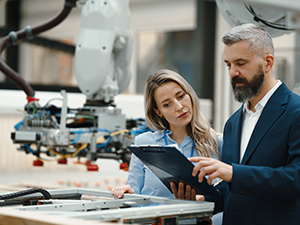
By Lori Runyan
VP of Program Management
In custom equipment design and manufacturing, precision and coordination are paramount. The development of schedules with key milestones and the management of critical paths are not just part of a to-do list; they are the lifeblood of success and customer satisfaction.
Clear and visible milestones provide stakeholders with a shared vision of progress and serve as a source of motivation for the entire team. When selecting milestones, it’s crucial to choose those that are easily understood and quantifiable, such as the completion of a critical component prototype, successful testing phases, and regulatory approvals.
These milestones become the foundation of schedule development and enable us to communicate progress effectively, make informed decisions, and ensure that everyone involved understands the project’s status.
As a senior executive, I emphasize the significance of these principles within our organization. By harnessing the power of well-crafted schedules and effectively managing critical paths while avoiding unnecessary details, we deliver high-quality custom equipment to our clients on time and within budget, meeting business objectives while exceeding customer expectations.
1. Understanding High-Level Stakeholder Perspectives
Let me illustrate the power of these principles with an example. We were engaged with a customer, and their senior vice president requested milestones for a complex project we were working on. We had a detailed schedule in place, but the SVP wanted visible milestones that would allow the client to drive the project at a high level, something tangible like seeing the robot in action.
It became clear that our existing milestones, which focused on testing phases and software development integrations, didn’t align with the SVP’s expectations. After all, you can’t see these behind-the-scenes activities until something tangible happens, like the equipment moving. The SVP was looking for milestones that resonated with their high-level objectives, ones that indicated progress on a scale they could relate to.
This situation highlighted a common challenge: terminology can mean different things to different people. What does a “milestone” really signify? To us, it might mean a successful software integration, but to our customer, it meant seeing the equipment perform at an incredibly precise level, such as system pump-down to the 10^-9th.
This experience taught us the importance of aligning our milestones with the customer’s perspective and objectives. It’s not enough to have milestones; they must be meaningful to all stakeholders. These milestones became project guideposts, providing a shared vision of progress and motivating the entire team.
Understanding the significance of clear and visible milestones, managing cross-functional dependencies, and maintaining focus on the big picture are essential in the world of custom equipment design and manufacturing. By tailoring our milestones to the customer’s viewpoint, we ensure that everyone comprehends the project’s status and works towards shared goals. This collaborative approach not only enhances our schedules but also strengthens our customer relationships and reinforces our commitment to delivering excellence.
2. Managing Interfaces Between People with Cross-Functional Task Dependencies
Just as it is critical to manage the interfaces between pieces of equipment, it is equally important to manage the interfaces between the people doing the work. In our complex custom equipment design projects, collaboration among various teams is essential. A mechanical engineer might rely on an electrical engineer, while engineering must align with purchasing to ensure the timely procurement of materials. Recognizing these dependencies and creating interfaces between responsible individuals is key to efficient project management.
For instance, when designing a piece of equipment, the mechanical and electrical engineering teams must collaborate closely. The mechanical engineer might need the electrical engineer to complete certain designs before they can integrate their components. Without clear task dependencies and interfaces, delays and bottlenecks can occur, jeopardizing project timelines.
3. Managing Dependencies & Critical Paths
Critical path management is a critical aspect of project scheduling. It identifies the sequence of tasks that, if delayed, will directly impact the project’s completion date. By recognizing these critical paths and the dependencies within them, we can allocate resources more effectively, minimize risks, and maintain project momentum.
To illustrate, consider the interplay between engineering and purchasing. If the purchasing team doesn’t secure the required materials on time, the entire project can grind to a halt. This underscores the importance of clear communication and coordination between these two functions, as well as the need to identify critical dependencies within their tasks.
4. Schedule Collaboration
A successful project schedule isn’t created in isolation. We often begin with a simple schedule, akin to a waterfall model, outlining key milestones and high-level task dependencies. This provides a foundational framework from which we can iterate and improve.
Team input is invaluable during this phase. We solicit feedback from all stakeholders to identify potential bottlenecks, refine task dependencies, and uncover parallel paths that can expedite project completion. This collaborative approach not only enhances the schedule but also fosters a sense of ownership and commitment among team members.
5. Avoiding Unnecessary Details & Embracing the Big Picture
It’s crucial to strike a balance in project scheduling. Too often, schedules get bogged down in unnecessary details, losing sight of the big picture and the critical path. While attention to detail is important, excessive focus on minor tasks can lead to micromanagement and inefficiency.
By maintaining a clear understanding of the critical path and key milestones, we can avoid the pitfall of overloading our schedules with minor tasks that do not significantly impact the project’s timeline. This allows us to stay agile, adapt to changes, and allocate resources where they truly matter.
6. The Illuminating Power of Less Obvious Milestones
While some milestones are highly visible, such as the completion of a prototype, there are other milestones that, although less apparent, prove enlightening. For instance, the moment when power is turned on, or when the equipment starts moving, can mark a significant step in our project. These milestones signify that our design has come to life, and they provide valuable insights into the functionality and performance of the equipment.
The Result: Increased Customer Satisfaction
In custom equipment design and manufacturing, the ability to develop schedules with clear and visible milestones, manage critical paths, and maintain focus on the big picture is instrumental to success. Recognizing the importance of cross-functional dependencies, interfaces between responsible parties, and the evolution of schedules through team input are also key to efficient project management and customer satisfaction.
Contact us to learn more about custom equipment design and build