How to Reduce Custom Automated Solution Costs by 30%
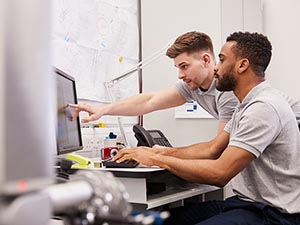
Imagine that your general manager challenges you to significantly reduce the cost of your current automation tool, and gives you three months to demonstrate the cost reduction results on a first-generation prototype. Never mind going to the purchasing group: the GM has already been there, and they have already driven supplier prices down as much as possible.
To meet competitive demands, your GM needs an additional 25% to 30% off the standard bill of materials, or the division won’t meet goal. You know that the only way to achieve that level of reduction is to redesign the basic platform of the tool; however, all of your engineering resources are overloaded with critical customer requests and roadmap commitments. You have strict constraints on hiring and no other group is going to volunteer their resources. You have no choice but to tell your GM there is no way you can meet his demand… but you know what kind of conversation that is going to be!
Sound familiar? This scenario is all too frequent and may have already happened to you. Your customers in semiconductors and other high tech markets are constantly demanding lower prices. This puts extreme pressure on all capital equipment suppliers to provide cutting-edge process technology at ever-lower costs. In order to remain competitive, your tool platform cost of goods sold must be reduced to support price reductions without sacrificing the gross margins needed to support your company’s profits.
The Problem
Why is it so hard to take cost out of an existing product? When the capital equipment manufacturer is confronted with the task of reducing product costs, the first attempt at cost reduction is usually targeted at their suppliers. In most cases, however, the supply chain organization has already stripped excess costs. Further reduction requires second sourcing or redesign for which there are limited resources. It then becomes obvious that the product cost is designed in, and system level redesign must occur to significantly affect total tool cost. On average, 80% of the cost of capital equipment is designed in and cannot be affected by supply chain efficiencies.
Part of the difficulty lies in the fact that most organizations have limited internal design resources. There is constant conflict over whether to apply engineering talent to roadmap commitments, urgent customer needs, or cost reduction programs. Usually, resources are allocated to meet customer commitments and support roadmap development.
Cost reduction is often something engineering is tasked with to be done “while you are at it,” and never adequately resourced. There is rarely any glory for reducing product costs, and the most talented engineers are seldom assigned to work on cost reduction programs if there are cutting-edge development projects to be done.
Suppliers can suggest lower cost alternatives for individual components, but opportunities are limited. It is not often that one component can be changed without affecting those surrounding it. Most suppliers do not have the system-level engineering talent or infrastructure to consider components they do not supply.
A Solution
The following is a case study describing a cost reduction effort conducted by Owens Design for a process tool platform. The customer needed a 30% cost reduction on the tool platform, while simultaneously implementing improvements in process technology. The cost reduction effort was conducted in a very low-risk manner, and all process-related components were exempted from consideration. The development timeframe was to deliver a first prototype of the cost reduced platform in three months to coincide with the process improvements.
The tool platform had been in high volume production for several years. As is typical in the industry, the platform was expanded with various options and upgrades to remain competitive over time. These changes were necessary to meet the requirements for next generation devices but added to the overall platform cost and component count.
Areas of particular interest for the cost reduction redesign focused on the following:
- Frame construction
- Electrical power and controls packaging
- Wire harnessing
- Pneumatics
- Cooling and heating systems
The first area of design focus concerned the general frame construction of the process module. The existing tool platform incorporated a standard tubular frame with a variety of separately build hardware and electrical enclosures that mounted directly to the frame. The new platform utilizes a folded sheet metal frame design with built-in enclosures and integral wire harness clips. This greatly reduces tool part count and eliminates the need for added enclosures and mounting brackets.
Major electrical and controls subsystems were reviewed, redundant components were eliminated, and remaining components were consolidated and collocated to reduce and simplify tool wiring. The new tool layout optimizes cable routing and is designed for pre-built wire harnesses to further reduce overall assembly labor.
The pneumatic control design and the heating and cooling systems for the tool were simplified. Each area was optimized with circuits being eliminated and consolidated, while still meeting functionality requirements.
In each area, maintainability, serviceability and manufacturability were also addressed, based on the input of the support organizations. This led to significant interest and participation in the project from the service, manufacturing and logistics organizations.
The result was that, in working in collaboration with the customer’s engineering group, all project metrics were met with an overall cost reduction of 30% and the first prototype was delivered in three months.
Partner with Owens Design for Tool Cost Reduction
While this describes a specific example, the same basic approach can be applied to many high-volume, complex, automated tool platforms. As an outside resource, Owens Design provides a fresh non-biased review of the current tool platform.
Your tool will be conceptually broken down to its lowest level in terms of required functionality. System layout of your tool will be optimized to meet the required functionality and balanced against the mandated cost targets. Tool frame construction and subsystem packing will be carefully reviewed, condensed and optimally located. Careful consideration will take place concerning part count and part cost. A bottom-up analysis will provide specific cost saving targets that can be used to determine whether implementing the design changes is cost-justified. If so, the design is detailed and prototypes will be built for design validation testing.