Reduce Risk & Accelerate Timelines for Custom Automation Projects: The Owens Design Phase 1
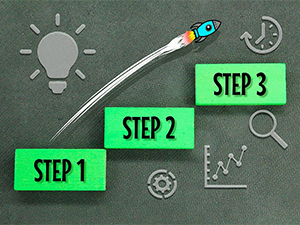
The success of custom OEM equipment design and factory automation projects depend as much on planning and strategy as it does execution.
The Phase 1 from Owens Design is a process for optimizing trade-offs, identifying critical dependencies, finding requirement gaps, and developing the system architecture for custom automation projects prior to detailed design, engineering and manufacturing. This helps reduce change orders, unnecessary costs, and scheduling delays
At the end of Phase 1, Owens Design will develop your concept into a product specification, complete with conceptual 3D models, detailed specification, software architecture, major component selection, costs, timelines, milestones, and instructions for mitigating known risks so you can move into the design and engineering phase with confidence.
An Owens Design Phase 1 also serves as a confidence builder for investors. Whether you are seeking seed funds or applying for government grants, a Phase 1 will provide you with a fixed price quote and road map for potential investors who will see a comprehensive plan and appealing return on investment (ROI) opportunity, so are more likely to provide funding and grants.
More about Phase 1 Benefits
Partnership Vetting
The Phase 1 allows your team to experience working with Owens Design designers, engineers, project management, and leadership. It starts the team building and collaboration process early, helping the combined team operate more efficiently and effectively. In general, it’s a way to lower risk and get your project moving and will also help you vet Owens Design should you be interested in continuing on with our design and build services as part of a Phase 2.
Design Trade-Off Identification
Tradeoffs in cost versus performance are almost always found as the design approach is solidified. Frequently unnoticed until the detailed concept is underway, they are a common source of unnecessary delays and can be reduced or eliminated as part of a Phase 1.
Critical Dependency Identification
Long lead-time items, software integration, and customer-supplied material or technical items are all critical dependencies that can be effectively managed when identified as part of a Phase 1.
Requirement Gap Identification
As your concept is detailed, any missing requirements or gaps in development skills of the team will be revealed. If they go undetected early in the process, they can lead to major delays or require redesign.
Project Risk Transfer
Following a successful Phase 1 and, once you have accepted a Phase II proposal, all project execution risk is then transferred to Owens Design. Delivering your custom automation equipment at a fixed price, meeting specified performance requirements, and adhering to the schedule are now our responsibility. This also eliminates potential delays from concept to the design and build process.
Phase 1 Deliverables
- A conceptual model of the complete system
- Hardware tool specification
- Functional description (theory of operation)
- Risk mitigation plan (if needed)
- Major components selection
- Electrical single line diagram
- Software function requirements specification and budgetary pricing for software development
- Prototype development schedule (hardware & software)
- Tool validation test plan
- Phase II proposal with fixed pricing for prototype and non-recurring engineering (NRE)
- Pricing estimates for volume production units
Is a Phase 1 Right for Your Project?
Every project in our 40 years of successful delivery started with a Phase 1. Contact an Owens Design team member today to discuss your project challenges, familiarize you through the process, and to see if a Phase 1 is right for your project.