Navigating the Automation Journey: Scaling Your Production Line Effectively
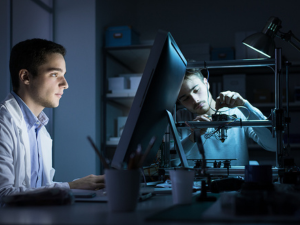
By Lori Runyan
VP of Program Management
In this article, I share insights gained from years in the manufacturing industry, particularly the critical transition from prototype development to full-scale production. This journey is both exciting and challenging, and understanding the stages of automation is key to successful scaling.
The article breaks down this journey into manageable stages, from manual workstations to fully integrated lines. Each stage offers unique advantages and challenges, tailored to different production needs and circumstances. Whether you’re just starting out with manual processes or aiming for a high-efficiency automated line, this piece provides valuable guidance for making informed decisions in scaling your production effectively.
In the world of manufacturing, the transition from prototype development to full-scale production can be both exciting and challenging. As companies and startups move from creating a successful working prototype to meeting the demands of a growing market, they often grapple with the question: “How do I scale my production?”
Unfortunately, there’s no one-size-fits-all answer to this question. The path to scaling production is a journey that can be broken down into several stages of automation, each catering to different needs and circumstances. In this article, we’ll explore the four stages of automation that can help you scale your production line effectively.
1. Manual Workstations
At the initial stage of scaling production, manual workstations are often the go-to choice. This approach is the simplest and easiest to scale because it involves human operators performing tasks with basic tools and equipment. In a manual workstation setup, additional workstations and staff can be added as needed to increase production capacity.
Manual workstations are particularly suitable for operations that require a high level of hand-eye coordination, such as precision wiring, PCB rework, and intricate medical device assembly. These tasks can be challenging to automate efficiently due to their complexity. Additionally, the decision to use manual workstations is influenced by labor costs, as it may be more cost-effective to employ skilled workers for these tasks.
One key advantage of manual workstations is their flexibility. They can adapt to changes in production requirements relatively easily, making them a practical choice for businesses in the early stages of scaling.
2. Manumation Stations
As production volumes increase, there comes a point when certain tasks become challenging for human operators to perform quickly or ergonomically. This is where “manumation” stations come into play. Manumation, a portmanteau of “manual” and “automation,” refers to a stage where some level of automation is introduced to streamline specific production steps.
In manumation stations, tasks that are difficult or time-consuming for human operators are partially automated. For example, imagine a workstation where multiple screws need to be inserted simultaneously. While parts are still manually loaded and unloaded, automation aids in the execution of intricate tasks. Manumation stations are a logical step toward automation in a production environment, enhancing efficiency and quality.
A few years ago, we were approached by a startup with a vision of diving headlong into full automation for a high-precision manufacturing process. Their eagerness was palpable, but so was the need for a measured approach. They trusted our advice so, instead of diving immediately into the deep end, we first set up manumation equipment to prove out their process. This phase was crucial, allowing us to fine-tune each step of their operation, which included critical tasks like gluing, laser processing, and assembly. It was during this stage that the true potential of a gradual scaling approach became evident.
By first establishing the process through manumation, we could identify and optimize key aspects of the production line. One significant benefit was our ability to introduce multiple lanes for parts of the process that took longer. This not only streamlined the workflow but also significantly enhanced overall process efficiency.
Once the process was refined and the client had a clear understanding of their production volumes, we confidently progressed towards more comprehensive automation solutions.
3. Islands of Automation
Islands of automation represent a more advanced stage in the automation journey. In this stage, a fully enclosed system consists of multiple automated steps within a single unit. The goal is to create a cohesive process that minimizes human intervention and maximizes efficiency.
Islands of automation are typically chosen for sequences of complex operations or to achieve higher throughput. For instance, consider a conveyor system equipped with adhesive dispensing, part placement, and UV curing – all integrated into one system. This setup enables a series of intricate steps to be performed seamlessly within a controlled environment.
One of the advantages of islands of automation is their ability to significantly boost productivity while maintaining a certain level of flexibility. However, they are still separate units, so a breakdown in one part of the system may lead to production delays.
4. Fully Integrated Line
The pinnacle of automation in production is the fully integrated line, where human intervention is virtually eliminated. In this stage, one machine seamlessly leads to another, creating a continuous, highly efficient production process. The fully integrated line is ideal for industries with the highest throughput requirements.
In a fully integrated line, each step is automated and tightly synchronized, ensuring a consistent and uninterrupted workflow. This level of automation is often found in industries such as automotive manufacturing, where precision, speed, and high volumes are paramount.
While a fully integrated line offers unparalleled efficiency, it comes with a trade-off in terms of flexibility. The entire system is interdependent, so any disruption or change in one part of the process can impact the entire production line. As a result, careful planning and redundancy measures are necessary to minimize downtime.
Choosing the Right Automation Stage
Selecting the appropriate stage of automation for your production line is a critical decision that should be based on various factors, including your product’s complexity, production volume, and budget constraints. Here are some key considerations to help guide your choice:
- Product Complexity: Evaluate the complexity of your product and the tasks involved in its production. Complex, highly customized products may benefit from manual workstations or manumation stations, where skilled operators can handle intricate tasks.
- Production Volume: Consider your production volume and growth projections. If you anticipate significant growth, islands of automation or a fully integrated line may be more suitable to meet increasing demand efficiently.
- Budget: Assess your budget and investment capabilities. While fully integrated lines offer high efficiency, they also require substantial capital investment. Make sure your budget aligns with your chosen automation stage.
- Flexibility: Examine your need for flexibility. If your production process requires frequent changes or adaptations, consider automation stages that offer greater flexibility, such as manual workstations or manumation stations.
- Industry Standards: Familiarize yourself with industry standards and best practices. Certain industries may have specific requirements or regulations that influence the choice of automation stage.
A Cautionary Tale
A Fortune 100 company that will remain unnamed, embarked on an ambitious project. They insisted on implementing a fully automated, lights-out production line for a new optics assembly. This decision, while technologically advanced, was premature given the product’s early stage in the market. When the product faced issues and was eventually not launched, the entire assembly line, which had been scaled too rapidly, had to be scrapped resulting in a huge capital loss. This scenario underscores the value of the more measured approach of islands of automation, allowing for incremental growth in line development that can scale and advance technically in concert with demand.
Choosing the Right Automation Stage for Your Production
The journey from prototype development to full-scale production can be both exciting and challenging. Understanding the four stages of automation—manual workstations, manumation stations, islands of automation, and fully integrated lines—can help you make informed decisions on how to scale your production effectively.
Remember that there is no one-size-fits-all solution, and the best automation stage for your production line depends on your specific circumstances and goals. Whether you start with manual workstations or aim for a fully integrated line, careful planning and strategic implementation are essential to achieving success in scaling your production.